There are nine key systems to support EMU to operating at high speed from 250-350Km/h. Among of them, four systems will use steel/iron/aluminum castings, including traction system, braking system, coupling system and bogies.
There are nine key systems to support EMU to operating at high speed from 250-350Km/h. Among of them, four systems will use steel/iron/aluminum castings, including traction system, braking system, coupling system and bogies.
Casting Aluminum
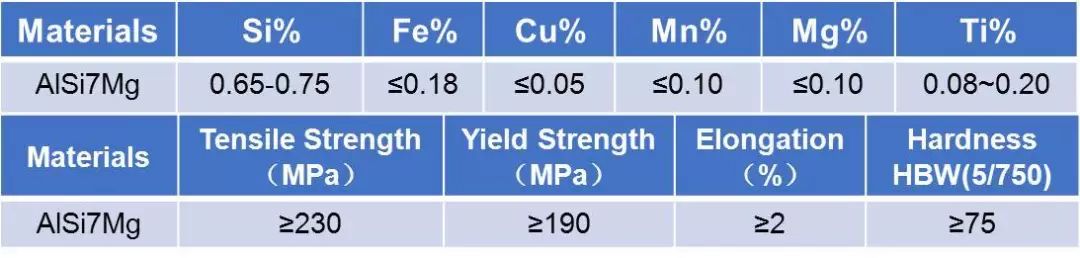
Casting Steels
Casting Iron
Gear Box (Casting Aluminum) - Shell
In traction systems, the most widely used aluminum castings are gear box. These pictures show the two kinds of gear boxes used for 350Km/h EMU. They have different structures and the bottom four pictures are traction systems after assembling. Each power bogie has two traction systems. Usually, the short-group (8 cars) EMU has eight power bogies. That means it needs 16 gear box castings. If for long-group (16 cars) EMU, the number of gear box castings will increase to 32.
Gear Box (Casting Aluminum) - Corbel
Size: 3166×1329×260mm
Weight: 660KG
Thickness: 18-125mm
25mm for average
Quality
☆ Internal quality: DR, 10% X-ray for key areas;
☆Exterior quality: as shown in the following sheet, any scull or chill mark is not allowed.
☆ Gear box casting for EMU are not allowed to do any welding repair in any area;
☆ Dimension tolerance: CT10-11;
☆ For finished surface: holes (≥1mm) are not allowed.
Braking System (Casting Steel)
Steel casting is most widely used in traction system, braking system, coupling system and bogies for EMU trains. Lots of parts as intermediate coupler, yoke, axle box, all kinds of clamps, support frame, axle mounted/wheel mounted brake disc, coupler fixture, bracket on the gear box, and other parts such as motor seat, center pin, center pin seat, are steel castings. No matter from type or quantity, steel casting is the most indispensable for EMU trains.
Quality
☆ The production of steel castings involves water glass sand casting, resin sand casting and investment casting;
☆Most of the cores are made of precoated-sand technology;
☆ Medium frequency furnace is generally used for melting, and some castings with high requirements need to be refined;
☆ The welding repair requirements should be under control and the welding repair operation needs to be carried out before final heat treatment;
☆ Some steel castings with high requirements need to be tested for gas content in steel, and welding repair is not allowed in key areas.
Braking System (Casting Steel)
Iron castings are usually used in braking cylinder and clamps, such as cylinder block, piston, coupling yoke, lever, frame and support crane. These castings are not very large in size. The average weight is about 20KG.
Quality
☆ The production of iron castings involves precoated-sand and resin sand process;
☆ Magnetic Particle Inspection was conducted at the rate of , which to ensure a high surface quality of casting;
☆ Casting defects repaired by mean of welding is not permitted.
Aluminum Castings - Gear Box
Heat treatment is also very important to microstructure manipulation and mechanical properties improvement for aluminum castings. Castings should be heated solution temperature and held for a certain time in heat-treatment furnace, and then quenching by water bath with the temperature of 60℃ ± 15. The time of transporting should be less than 40s.
Steel castings
Steel casting process is the semi-automatic ester hardened water glass production line. Intermediate frequency induction furnace is used for melting.
Iron castings
For casting iron, furan sand process is used because of better strength of sand mold, which make the casting has better surface quality and dimension tolerance. Shell sand core is also widely used for iron castings.
For next generation EMU, the weight is the most concerned because to achieve higher speed, for example 400km/h, the EMU should have weight limitation and less weight also can save more energy. So, the castings for EMU should be much lighter. Besides to do some optimizations in designing of casting, choose light metals and alloys for castings is a very important method. For processing of casting, 3D-printing technology is widely used for casting prototype and more intelligent and green manufacturing processes are used for castings.
Magnesium Alloy for Gear Box
The magnesium alloy gear box is only 50Kg, 33% less in weight. This gear box is also manufactured with low pressure sand casting process.
3D-printing Technology
In the traditional process for casting, mold manufacturing will cost long time, but with 3D-printing, sand mold and core can be manufactured in a short time. It will save more time for us to get the casting prototype to help the designer to do type testing and optimize the designing. Also we can even produce castings without mold for some parts with small batch.
Intelligent & Green Manufacturing - Low Pressure Permanent Mould Casting
Compared with low pressure sand casting, permanent mould casting has some advantages such as: better surface roughness and lower dimension tolerance, better mechanical properties because of higher cooling speed. The facility is more intelligent and automatic, together with better working environment.
(Data and pictures in this article come from the "Present situation and future development trend of casting manufacturing technology for high speed EMU" report given by Dr. Xia Shaohua, vice director in Materials Technology R&D Center of CRRC Qishuyan Institute Co., Ltd.)
Contact Us:
For Thailand & other ASEAN countries:
59 Dawn Corp Co., Ltd.
Mr. Sunart Viriyangkul
Mobile: + 66 81 875-4455
Email: metalAP@gmail.com
For Other Countries/Areas:
FPC & FICMES
Ms. Gillian Li
Tel: 86 13624029805
Email:lmt@foundrynations.com
Ms. Lydia Huang
Tel: 86 13816099095
Email: Lydia.huang@foundrynations.com